Plastic extrusion for large-scale custom plastic parts
Plastic extrusion for large-scale custom plastic parts
Blog Article
Recognizing the Basics and Applications of Plastic Extrusion in Modern Manufacturing
In the world of modern-day production, the strategy of plastic extrusion plays an instrumental role. Unwinding the principles of this procedure discloses the real convenience and potential of plastic extrusion.
The Fundamentals of Plastic Extrusion Process
While it may appear complicated, the basics of the plastic extrusion procedure are based upon reasonably uncomplicated principles. It is a manufacturing process in which plastic is thawed and afterwards formed into a constant profile with a die. The raw plastic product, usually in the kind of pellets, is fed right into an extruder. Inside the extruder, the plastic is subjected to warmth and stress, creating it to thaw. The liquified plastic is after that required with a shaped opening, understood as a die, to develop a long, constant product. The extruded product is cooled down and after that reduced to the preferred length. The plastic extrusion process is extensively used in various industries due to its convenience, performance, and cost-effectiveness.
Different Kinds of Plastic Extrusion Techniques
Building upon the fundamental understanding of the plastic extrusion procedure, it is necessary to explore the numerous strategies entailed in this production technique. In contrast, sheet extrusion produces big, level sheets of plastic, which are generally further processed into products such as food product packaging, shower drapes, and auto components. Understanding these strategies is essential to making use of plastic extrusion effectively in modern-day production.

The Duty of Plastic Extrusion in the Automotive Market
A frustrating bulk of parts in contemporary lorries are items of the plastic extrusion process. Plastic extrusion is primarily utilized in the production of different auto components such as bumpers, grills, door panels, and dashboard trim. Hence, plastic extrusion plays a critical function in auto production.
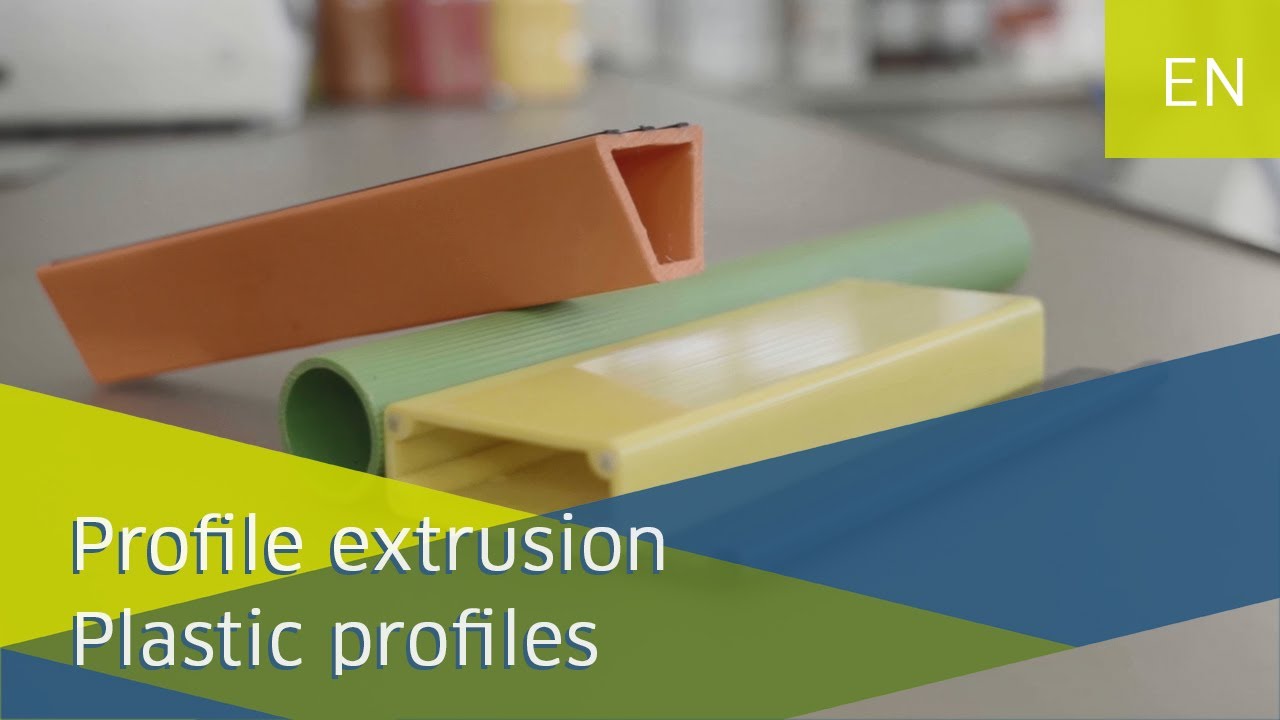
Applications of Plastic Extrusion in Consumer Goods Manufacturing
Past its substantial impact on the auto industry, plastic extrusion shows just as effective in the realm of customer goods producing. The versatility of plastic extrusion enables suppliers to make and create intricate forms and sizes with high precision and effectiveness. The adaptability, flexibility, and cost-effectiveness of plastic extrusion make it a preferred option for lots of customer items manufacturers, contributing significantly to the sector's development and innovation.
Environmental Effect and Sustainability in Plastic Extrusion
The prevalent usage of plastic extrusion in making welcomes analysis of its eco-friendly effects. As a procedure that regularly uses non-biodegradable materials, the environmental impact can be significant. Energy intake, original site waste manufacturing, and carbon exhausts are all problems. Nonetheless, sector improvements are boosting sustainability. Effective machinery reduces energy usage, while waste monitoring systems reuse scrap plastic, decreasing basic material demands. Additionally, the development of biodegradable plastics supplies an extra ecologically friendly alternative. Despite these renovations, additionally advancement is needed to mitigate the ecological impact of plastic extrusion. As society leans in the direction of sustainability, suppliers have to adapt to remain viable, stressing the value of continuous research and innovation in this field.
Final thought
Finally, plastic extrusion plays a critical function in modern-day manufacturing, specifically in the automobile and customer goods markets. Its flexibility permits the manufacturing of a wide variety of components with high precision. In addition, its potential for reusing and development of naturally degradable products offers an appealing method towards lasting techniques, thus attending to ecological concerns. Comprehending the essentials of this process is essential to enhancing its advantages and applications.
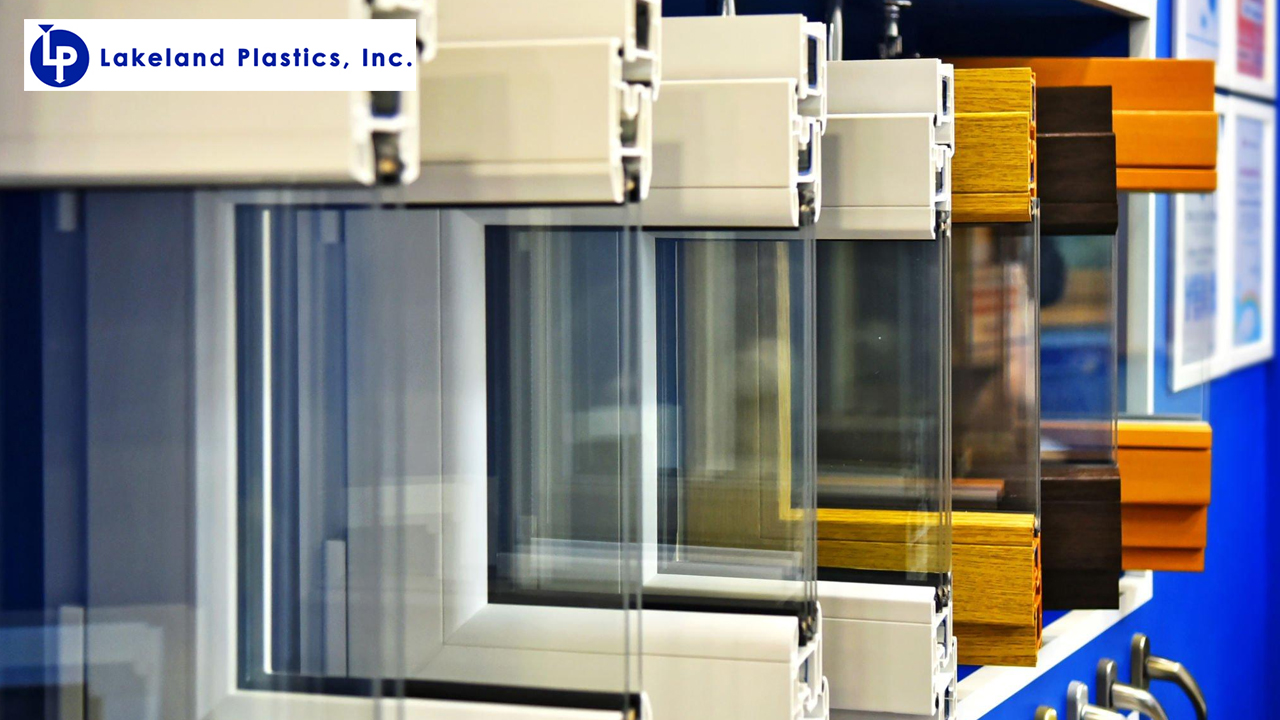
The plastic extrusion procedure is extensively used in various sectors due to its effectiveness, cost-effectiveness, and versatility.
Building upon the basic understanding of the plastic extrusion procedure, it is required to explore the numerous techniques entailed in this manufacturing method. websites plastic extrusion. In comparison, sheet extrusion creates huge, flat sheets of plastic, which are typically more processed right into products such as food product packaging, shower curtains, and auto parts.A frustrating majority of components go to my site in modern lorries are products of the plastic extrusion procedure
Report this page